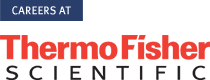
Job Information
ThermoFisher Scientific Set-up Technician - Nights in High Point, North Carolina
Work Schedule
12 hr shift/nights
Environmental Conditions
Cleanroom: no hair products, jewelry, makeup, nail polish, perfume, exposed piercings, facial hair etc... allowed
Job Description
Set Up
Our employees share a common set of values - Integrity, Intensity, Innovation and Involvement. Our ability to grow year after year is driven by our ability to attract, develop and retain world-class people who will thrive in our environment and share in our desire to improve humankind by enabling our customers to make the world healthier, cleaner and safer.
As one team of 100,000+ colleagues, we are working together to accelerate research, solve complex scientific challenges, drive technological innovation and support patients in need. #StartYourStory at Thermo Fisher Scientific, where diverse experiences, backgrounds and perspectives are valued.
Working Shift: Nights // 7:00pm - 7:00am (2-2-3 schedule)
Incredible Benefits!
Medical, Dental, and Vision – effective day1
Paid time off and holidays
401k company match up to 6%
Tuition Reimbursement – available after 90 days
Employee referral bonus
Employee discount program
Employee recognition program
Charitable gift matching
Company paid parental leave
Career advancement opportunities
Ensures the proper set up and operation of the encapsulation machinery.
Essential duties and responsibilities
At the start of the shift, performs check of all products and understands when change overs will occur and prepares for change overs.
Checks the actual operation of all lines at the start of the shift and periodically throughout the shift. Checks the quality of the product and makes adjustments as needed.
Reviews all paperwork to ensure completeness and accuracy. Also, checks paperwork on tanks. Ensures all required quality checks are being completed according to work instructions. Performs all checks as required and documents activities.
Prepares for, assists with, and monitors the execution of changeovers. This includes insuring the correct materials and equipment are available. Upon completion of the changeover, completes all required paperwork and obtains approval.
Responsible for cleaning equipment as required and ensures that equipment is visually clean and documented properly before use.
Assists with cleaning of the Encapsulation area and any duties as needed. May be required to perform other reasonable, related business duties.
Assists with the training of operators to enhance team performance and to increase personal knowledge of Encapsulation.
Informs Lead Operators and Operators of all adjustments made to the machine to ensure quality at all times. Adjustments may include something as simple as temperature adjustments after a gel change.
Assist Lead Operators and Operators to determine reasons for machine problems and make repairs.
Qualifications
To perform this job successfully, an individual must be able to perform each essential duty satisfactorily. Additionally, an individual must uphold the standards of conduct of the company, which include confidentiality, cooperation and respect for people and property. The requirements listed below are representative of the knowledge, skill and/or ability required. Reasonable accommodations may be made to enable individuals with disabilities to perform the essential functions.
Education and experience:
High school diploma or GED and six months to one year related experience.
Language skills:
Ability to read a limited number of two- and three-syllable words and to recognize similarities and differences between words and between series of numbers. Ability to print and speak simple sentences and to make entries in logbooks and on check sheets. Ability to read and comprehend simple instructions, safety rules, operating and maintenance instructions, procedures and policies, short correspondence, and memos. Ability to effectively present information in one-on-one and small group situations to customers, clients and other employees of the organization.
Ability to write simple correspondence, reports and complete required paperwork. Ability to understand and implement management directives.
Mathematical skills:
Ability to add and subtract two digit numbers and to multiply and divide with 10’s and 100’s.
Ability to add and subtract in all units of measure, including time, volume, weight and distance, using whole numbers, common fractions and decimals. Ability to apply concepts such as fractions, percentages, ratios and proportions to practical situations. Ability to draw and interpret bar graphs, compute rate, ratio and percent.
Reasoning ability:
Ability to apply common sense understanding to carry out detailed uninvolved written, oral or diagram instructions. Ability to deal with problems involving several concrete variables in standardized situations. Ability to solve practical problems and deal with a variety of concrete variables in situations where only limited standardization exists.
Other skills and abilities:
Ability to use measuring instruments and simple hand tools. Ability to be attentive to task at hand. Ability to understand and follow management and supervisory directives. Ability to plan ahead, organize and other project management skills. Demonstrated mechanical ability. Ability to perform all duties required of an Operator.
Certificates, licenses, registrations
None required.
Special requirements
Must meet applicable DEA security clearance requirements.
PHYSICAL DEMANDS
The physical demands described here are representative of those that must be met by an employee to successfully perform the essential functions of the job. Reasonable accommodations may be made to enable individuals with disabilities to perform the essential function.
While performing the essential duties of this job the employee is occasionally required walk, climb, balance and talk/hear/listen (communicate with others). The employee is frequently required to stand, stoop, kneel, crouch and crawl. The employee is regularly required to use hands to finger, handle or feel, reach with hands and arms, and to perform overhead lifting and reaching. The employee must be able to frequently push/pull/lift/carry up to 50 pounds. Heaviest exertion is experienced when moving tanks of gelatin or medicine using hand pallet. Specific vision requirements include close vision, color vision, peripheral vision and the ability to adjust focus.
Work environment
The employee regularly works near moving mechanical parts. The employee may be exposed to vibrations and to wet or humid indoor conditions. The noise level is moderate to loud.
Personal protective equipment
Lab coat or uniform, safety glasses, safety shoes, gloves, hair protection, ear plugs.
Thermo Fisher Scientific is an EEO/Affirmative Action Employer and does not discriminate on the basis of race, color, religion, sex, sexual orientation, gender identity, national origin, protected veteran status, disability or any other legally protected status.