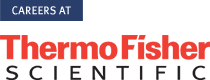
Job Information
ThermoFisher Scientific Supervisor, Mfg Equipment Maintenance - 2nd shift in Allentown, Pennsylvania
Work Schedule
Second Shift (Afternoons)
Environmental Conditions
Able to lift 40 lbs. without assistance, Adherence to all Good Manufacturing Practices (GMP) Safety Standards, Cleanroom: no hair products, jewelry, makeup, nail polish, perfume, exposed piercings, facial hair etc... allowed, Cold Room/Freezers -22degrees, Office, Some degree of PPE (Personal Protective Equipment) required (safety glasses, gowning, gloves, lab coat, ear plugs etc.)
Job Description
When you are part of the team at Thermo Fisher Scientific, you’ll do important work, like helping customers in finding cures for cancer, protecting the environment or making sure our food is safe. Your work will have real-world impact, and you’ll be supported in achieving your career goals.
Fisher Clinical Services, part of Thermo Fisher Scientific, is a leading provider of global clinical supply chain. With unwavering commitment to service, science and process engineering, Fisher Clinical Services is powered by people with an exceptional commitment to quality, deeply instilled ethics of personal responsibility and unrivaled expertise. We are exclusively focused on serving the packaging and distribution requirements of clients across the world. Whether planning, packaging, labeling, storing, or distributing important supplies, Fisher Clinical Services has been committed to delivering the highest possible value while ensuring adherence to the highest level of quality, performance, reliability and sustainability standards. http://www.fisherclinicalservices.com/
Location/Division Specific Information
CTD partners with pharmaceutical and biotech customers around the world to ensure the right patients get the right therapies in the right doses at the right time – a concept that we internally embrace as “There is a Patient Waiting.” Our unique blend of services includes project management, packaging, distribution, transportation management and specialty logistics, ancillary supply management, clinical supply optimization, bio-repository storage and much more. Our more than 3000 employees in over 15 countries work hard every day knowing that what they do matters.
How will you make an impact?
As part of our team, what you do contributes directly to our mission; enabling our customers to make the world healthier, cleaner and safer.
What will you do?
The Team Leader, Technical Operations is responsible for identifying equipment/process problems and improvement opportunities in the primary and secondary packaging operations. This role requires mechanical proficiency, diagnostic and problem-solving abilities, strong technical writing skills, and the ability to communicate both verbally and written. The individual will work independently and provide leadership to the Technical Operators and be the Subject Matter Expert (SME) on all equipment in packaging. They will work closely with Packaging Management to ensure efficiency and improvements are achieved on the equipment/process. They will create/update Change Controls, Deviation Investigations and SOPs for improvements, audit observations, corrective and preventative actions, and to maintain compliance with periodic reviews. They assist in problem solving and long-term continuous improvements with the Operations team, Engineering, Quality Assurance, and Information Technology departments.
How will you get here?
Education
High School Diploma or GED, with a minimum of 6 years prior mechanical and process equipment experience in a GxP production environment. Associate or Bachelor degree preferred.
Responsibilities
Supervise up to 10 employees working on multiple production lines in a clinical pharmaceutical manufacturing/packaging environment.
Apply Good Manufacturing Principles in all areas of responsibility.
Remain informed about business deliverables and priorities and create staff schedule to support setup, repair, predictive and preventative maintenance among other activities.
Monitor equipment trends.
Ensure adequate coverage and response in an environment where priorities may change.
Troubleshoot equipment setups and repairs as first frontline SME.
Write equipment procedures (SOPs).
Write investigations pertaining to equipment process and failures.
Review equipment documentation.
Performs new equipment Preventive Assessments.
Maintain equipment and components inventory quantities.
Responsible for process improvement and risk assessments regarding equipment processes.
Responsible for supporting Operations staff on delivering and meeting schedule timelines.
Responsible for supporting Process Engineering on diagnosis and repair of equipment.
Responsible for supporting equipment calibration or performing it.
Sustain a strong safety culture, every day.
Conduct training for Technical Operations and Process Technicians on their duties, company policies, and procedures.
Perform coaching and evaluation of Technical Operators and Process Technicians.
Assess technical development needs of staff and create plans to continually enhance abilities and discernment.
Act in a professional and approachable manner. Possess stronginterpersonal, listening and communication skills. Work collaboratively, and in tandem with peer Production leaders.
Demonstrate and promote the company vision of the 4 I’s: Integrity,Intensity,Innovation, and Involvement. Act as a role model leader.
Apply Good Manufacturing Principles in all areas of responsibility.
Investigate and write process deviations, identify root causes, and implement corrective actions.
Write Change Controls pertaining to equipment projects.
Performs other duties as assigned to meet the needs of business.
Knowledge, Skills, Abilities
Mechanical, electrical, or equivalent experience preferred.
Strong level of mechanical ability to be assessed by testing.
A minimum of 1 year of progressive people management and leadership experience, serving as a role model for diversity and inclusion.
Strong technical writing skills and ability to create Standard Operating Procedures, technical documentation, and communication memos.
5 years + in equipment repair and preventative maintenance.
2 years + leading or self-directing including preventative maintenance scheduling.
Provenability to work with minimal supervision and accuratelyprioritize multiple tasks.
Experience or familiarity with Maximo asset management software preferred.
Microsoft Word and Outlook experience preferred.
Mastery of skills required to read, understand, and adhere to the SOPs and policies of a GMP environment.
Knowledge of Quality systems and standards.
Familiarity with Engineering principles and practices.
Familiarity with of human resources practices.
Ability to think critically and problem solve.
Decision making skills.
Communication and influence skills.
Conflict Management abilities.
Cultivation of collaboration and teamwork.
Adaptability, and ability to multi-task in an environment where priorities may change daily.
Ability to work overtime
Ability to work different shifts at time
Physical Requirements
Lifting, standing, sitting, walking, and squatting. Ability to lift and load up to 70 pounds of materials onto a machine.
The position is exposed to cold temperatures, below 32 degrees, for more than one hour at a time. The position will be exposed to atmospheric conditions could require special personal protection equipment.
Vision requirements for this position: close vision (clear vision at 20 inches or less), distance vision (clear vision at 20 feet or more), color vision, peripheral vision (ability to observe an area that can be seen up and down or to the left and right while eyes are fixed on a given point), depth perception (three-dimensional vision) and the ability to adjust focus.
Incumbent must meet applicable visual acuity/color blindness standards.
Personal Protective Equipment Certification (PPE) including but not limited to filtering face masks, PAPR, N-95 masks, half face masks, and safety glasses is required to perform this position.
Join us and contribute to our singular mission—enabling our customers to make the world healthier, cleaner and safer.
Apply today! http://jobs.thermofisher.com
Thermo Fisher Scientific is an EEO/Affirmative Action Employer and does not discriminate on the basis of race, color, religion, sex, sexual orientation, gender identity, national origin, protected veteran status, disability or any other legally protected status.
Accessibility/Disability Access: We will ensure that individuals with disabilities are provided reasonable accommodation to participate in the job application or interview process, to perform essential job functions, and to receive other benefits and privileges of employment. Please contact us to request accommodation.
Thermo Fisher Scientific is an EEO/Affirmative Action Employer and does not discriminate on the basis of race, color, religion, sex, sexual orientation, gender identity, national origin, protected veteran status, disability or any other legally protected status.